Unlocking Success: Labor Cost Management in the Auto Industry
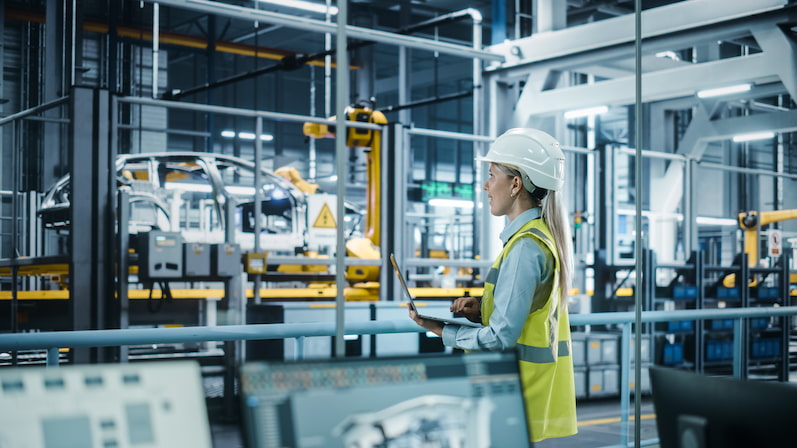
Advanced scheduling solutions offer up to 21% in labor cost reductions.
Maintaining a competitive edge is imperative for business in the automotive manufacturing industry. Competition has grown as auto companies grapple with high inflation rates and rising materials costs. As the cost to consumers has increased, industry players have had to compete harder for business and get creative with other approaches to offset steeper materials prices.
Furthermore, the auto industry is dramatically transforming, fueled by rapid technological advancements and evolving consumer demands. This shift creates a high-stakes environment where efficiency and agility are necessary for survival. For instance, there is growing pressure to accelerate electric vehicle (EV) development, driven by regulatory changes and government initiatives across the globe. According to PwC, the EV market in the US is expected to increase by a staggering 30% by 2030.
But in today’s market, EVs remain expensive to manufacture primarily because of the costs associated with their EV batteries. Additionally, the advanced technology and infrastructure needed for manufacturing EVs, including the design and development of electric powertrains and charging systems, contribute to the higher production costs.
With increasing pressure to manage costs to align with consumer demands, manufacturers are compelled to continually refine their processes and streamline operations. Even marginal improvements can have a significant influence on the bottom line. That’s why optimal management of labor costs presents substantial opportunities for savings.
Shift scheduling challenges
Since the pandemic, the auto industry has not been immune to staffing obstacles, with attrition becoming particularly problematic in recent years. These challenges extend beyond mere financial costs, significantly affecting operational efficiency. When shifts start late or workers are misassigned to tasks beyond their expertise, productivity suffers markedly.
Productivity continues to suffer from disorganized shift scheduling when working hours are spent on incidental, non-essential tasks. Take idle time (the time that employees are clocked in but not productive) for example. Reducing idle time and ensuring that employees are maintaining productivity helps improve the bottom line.
Furthermore, staffing complications deteriorate production quality and elevate the risk of errors. Such manufacturing missteps can spiral into expensive reworks and recalls—every manufacturer’s nightmare scenario. The fallout from these errors is not just disruptive but potentially catastrophic, with losses that can soar into the millions, severely threatening a company’s financial stability.
Recommended: 5 Ways to Increase Workforce Agility to Meet Your Production Targets
Scheduling for OEMs in the auto industry remains an especially difficult challenge. Shift scheduling is more than just filling out a timetable; it’s about strategically placing workers to maximize ergonomics, safety, and efficiency. OEMs must also ensure that employees remain alert and engaged, which requires a complex rotation schedule that accounts for the different skill sets and certifications each team member brings.
To make scheduling more complicated, workers must be fully trained and continually update their skills to ensure the company complies with regulations.
Ongoing labor negotiations and staffing shortages have also highlighted the need for employers to factor in employee preferences, especially with scheduling. Satisfying workers’ desires for more schedule autonomy doesn’t have to conflict with employers’ desire to succeed in the market. Organizations are learning that being responsive to workers’ needs and providing flexibility can be compatible with the drive toward efficiency and quality in several important ways.
Unlocking an untapped opportunity: minimizing labor costs with scheduling software
Advanced scheduling software solutions have become indispensable in the automotive OEM industry, where optimization and agility are paramount. These tools are unlocking an untapped opportunity for cost savings, transforming the complexities of labor management into avenues for enhanced productivity and operational excellence.
Adopting advanced scheduling is more than a technological upgrade; it’s a strategic move towards a more adaptable, efficient, and worker-friendly manufacturing environment. By integrating these innovative scheduling solutions, OEMs can position themselves at the forefront of the industry, capitalizing on innovative ways to streamline operations and reduce expenses.
Furthermore, implementing advanced scheduling solutions is pivotal in scaling cost-saving measures across entire operations. These tools ensure optimal human resource allocation by emphasizing scheduling efficiency, coverage optimization, and strategic cost-cutting. This approach not only minimizes downtime and excess labor costs but also significantly enhances the ability of manufacturers to manage costs effectively at scale, offering up to 21% in labor cost reductions because of several notable benefits:
- Optimized staffing: Scheduling software can automatically assign workers to shifts based on their skill sets and certifications, ensuring that every critical position is covered by a qualified individual. This prevents situations where work slows down because a worker with a necessary skill is not on shift. In turn, this decreases idle time by enhancing time that is invested into meaningful work.
- Ergonomic rotation: To prevent worker fatigue and the associated decline in productivity, scheduling software can rotate employees through various tasks. This keeps workers alert and engaged while also helping to reduce the risk of repetitive strain injuries, which can lead to absences and reduced workforce efficiency.
- Compliance tracking: Software can monitor training and certification renewals, alerting managers to upcoming expiration dates to ensure workers are always compliant with industry regulations. This proactive approach is crucial for avoiding production stoppages and managing compliance efficiently at scale.
- Demand forecasting: By analyzing production schedules and historical demand, scheduling software can forecast staffing needs, allowing OEMs to adjust their labor force in real time, reducing overtime costs while balancing staffing availability and preferences.
- Reduced administrative time: Automated scheduling reduces the time managers spend on creating and managing shift schedules, allowing them to focus on more value-added activities.
- Improved communication: Many scheduling solutions allow for real-time updates and notifications for workers, reducing miscommunication.
- Flexibility and employee satisfaction: By accommodating individual worker preferences where possible, scheduling software can increase job satisfaction, reduce turnover, and improve efficiency.
For manufacturers in the automotive space, maintaining a competitive edge is not just about innovation and quality; it’s also about driving operational changes that decrease idle time and reduce costs by maximizing labor hours. Phil Duncan, a former automotive executive, sums it up succinctly: “Efficiently minimizing non-essential tasks and maximizing value-added work translates to reduced costs.” This statement encapsulates labor cost management—it’s about minimizing non-essential tasks and amplifying each worker’s contributions.
As the automotive industry accelerates toward new technologies and innovations, labor cost management through shift scheduling will play a key role in managing costs and building a resilient, high-performing workforce that can drive the industry forward.
Advanced scheduling software is pivotal in managing labor costs effectively and is key in building a resilient, high-performing workforce. By optimizing shift scheduling, manufacturers can respond more dynamically to the challenges of the market, ensuring both cost efficiency and the agility to drive the industry forward.
This article was first published in evdesignandmanufacturing.com.